Are you looking for ways to streamline your manufacturing operations and enhance overall efficiency? Manufacturing ERP solutions could be the answer. These software systems are specifically designed to meet the unique needs of manufacturing businesses, providing a centralized platform for data management and analysis.
Manufacturing ERP systems bring together different aspects of business operations, such as production, inventory management, and supply chain management. They're equipped with a wide range of features to enhance the way your business functions, but how exactly do they do this?
Let's explore the impact of ERP systems on the manufacturing industry and highlight their benefits in streamlining operations and enhancing efficiency.
Key Takeaways:
- Manufacturing ERP systems are software solutions designed for manufacturing businesses.
- They offer a centralized platform for data management and analysis.
- ERP systems integrate various operational facets including production, inventory management, and supply chain coordination.
- Manufacturing ERP systems streamline operations and enhance efficiency.
- Benefits of ERP software include enhanced efficiency, improved decision-making, cost savings, and scalability.
What is Manufacturing ERP (Enterprise Resource Planning)?
Manufacturing ERP (Enterprise Resource Planning) software systems are essential tools designed to integrate and streamline the core business processes of manufacturing companies.
By integrating key areas such as production scheduling, inventory management, and supply chain operations into a one unified ERP platform, they offer a comprehensive approach to managing the complexities of modern manufacturing environments.
They automate processes, thereby increasing efficiency and providing real-time visibility into every facet of the business.
Standard vs Manufacturer (MRP VS ERP)
The distinction between MRP and ERP is important. While both systems serve the needs of manufacturers, there are key differences that make each one suitable for different types of businesses.
MRP platforms are designed specifically for production planning and inventory management. They are typically used by smaller manufacturers with simpler production processes.
These systems provide businesses with the tools to effectively manage their inventory levels, streamline production planning, and ensure efficient material requirements. However, MRP systems have a narrower focus and may not offer the comprehensive functionality required by larger manufacturers.
On the other hand, generic ERP systems offer a more extensive solution that integrates various aspects of operations within a manufacturing business. They provide capabilities beyond production planning and inventory management, including supply chain coordination, financial management, customer relationship management, and more.
ERP systems are better suited for larger manufacturers with complex operations and the need for a centralized platform for data management and analysis.
The distinction between MRP and ERP lies in the breadth of functionality and integration offered by each system. MRP systems are focused on the core aspects of production planning and inventory management, making them suitable for smaller manufacturers.
ERP systems, in contrast, provide a comprehensive solution that addresses the broader needs of manufacturers and are better suited for larger businesses.
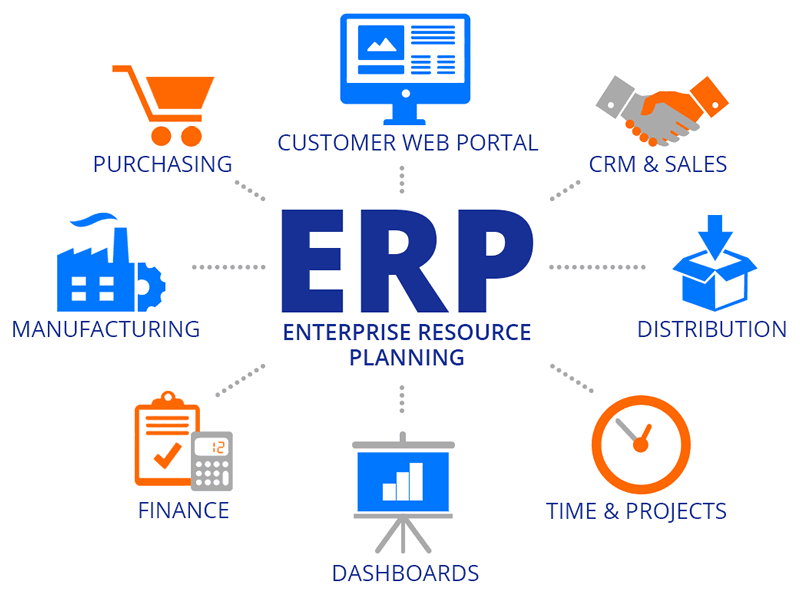
Key Features of a Manufacturing ERP System
Manufacturing ERP systems offer a range of key features that help businesses efficiently manage their operations. These include:
Inventory Management
ERP software solutions provide real-time tracking of inventory levels, allowing businesses to monitor stock levels and make informed decisions regarding reorder points. Automated reordering functionality streamlines the purchasing process, ensuring that inventory levels are always optimized.
Additionally, cost control measures enable businesses to analyze and reduce inventory holding costs, improving overall inventory management.
Supply Chain Management
Streamlining the supply chain is crucial for manufacturing businesses. ERP systems offer features that enhance supplier collaboration, enabling businesses to communicate and coordinate with suppliers in real-time.
These systems also facilitate demand forecasting, enabling businesses to accurately predict customer demand and optimize inventory levels throughout the supply chain. By implementing ERP systems, businesses can achieve greater visibility and control over their supply chain, resulting in improved efficiency and cost-effectiveness.
Production Planning and Scheduling
Efficient production planning and scheduling are essential for meeting customer demand and optimizing resource utilization. ERP systems enable businesses to create production schedules based on real-time data and demand forecasts.
These systems also optimize resource allocation, ensuring that materials, machines, and labor are effectively coordinated. Real-time monitoring capabilities allow businesses to track production progress, identify bottlenecks, and make necessary adjustments to maintain efficient production processes.
Quality Control and Compliance
Ensuring product quality and compliance with industry regulations is paramount for manufacturing businesses. ERP systems provide features that enforce quality standards throughout the production process. These systems allow businesses to track product quality, implement quality control measures, and identify and resolve quality-related issues promptly.
Additionally, ERP systems assist in regulatory compliance by providing documentation and traceability, enabling businesses to meet industry-specific compliance requirements and maintain consistent product quality.
Benefits of ERP in the Manufacturing Industry
Why do manufacturing companies need ERP functionality? Implementing an ERP system in your manufacturing business offers numerous benefits that can significantly enhance your operations and contribute to your overall success.
Enhanced Efficiency
- Automated processes: ERP streamlines manual tasks, reducing the need for manual labor and increasing efficiency.
- Minimized errors: By automating processes and generating real-time data, these systems help minimize human errors, leading to improved productivity.
- Centralized data management: ERP technology provide a centralized platform for data management, eliminating the need for multiple systems and reducing data redundancy.
Improved Decision-Making
- Real-time business visibility: ERP provides real-time access to accurate data, allowing you to make informed decisions based on current information.
- Data-driven insights: With detailed reporting and analytics capabilities, ERP systems enable data-driven decision-making, empowering you to identify trends, forecast demand, and optimize production.
- Streamlined communication: This technology facilitates seamless communication and collaboration across departments, ensuring that information flows accurately and efficiently.
Cost Savings
- Optimized inventory management: ERP systems provide real-time inventory tracking, ensuring optimal inventory levels, reducing carrying costs, and preventing stockouts.
- Efficient resource allocation: By optimizing production planning and scheduling, ERP helps allocate resources effectively, minimizing waste and lowering costs.
- Minimized production downtime: With real-time monitoring and maintenance capabilities, it reduces equipment breakdowns and production disruptions, leading to cost savings.
Scalability
- Adaptable to growth: ERP software can grow and adapt with your business, accommodating increased production needs, expanding operations, and supporting your long-term growth strategy.
- Flexible customization: They offer customization options to meet your specific manufacturing requirements, ensuring that the software aligns with your unique business needs.
- Support for multiple locations: If you have multiple manufacturing facilities or global operations, ERP provides
Notably, headless ERP systems excel in scalability, allowing businesses to easily add or modify functionalities without disrupting the core system, making them an excellent choice for businesses planning significant growth.
By leveraging the benefits of ERP in manufacturing, you can optimize your production processes, improve decision-making, achieve cost savings, and position your business for sustained growth and success in the competitive manufacturing industry.
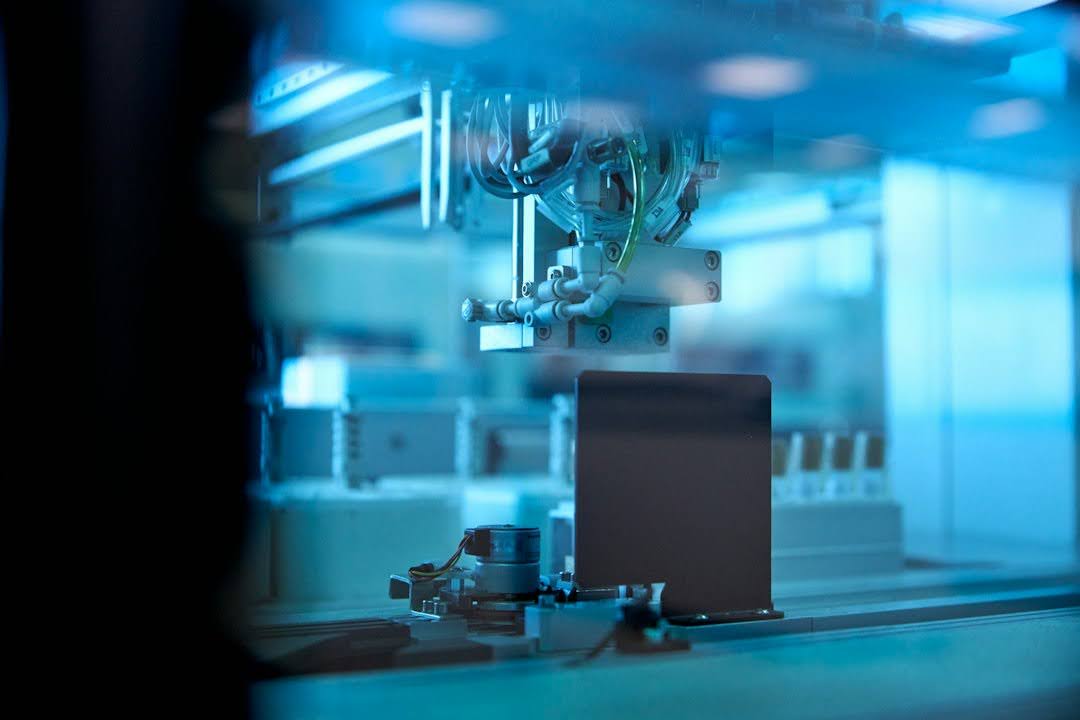
The Different Types of ERP Solutions
When it comes to selecting the best manufacturing ERP system, there are several options to consider. Each option has its own advantages and considerations that need to be evaluated based on your unique business needs.
In this section, we will explore three types of ERP systems commonly used in the manufacturing industry: on-premise ERP, cloud-based ERP, and hybrid ERP. Additionally, we will outline key considerations to keep in mind when selecting the right ERP system for your manufacturing business.
On-Premise ERP
An on-premise ERP system is installed and maintained on-site within your organization's infrastructure. This type of ERP solution offers greater control and customization capabilities, allowing you to tailor the system to your specific manufacturing processes.
However, it requires higher upfront costs for hardware, software licenses, and IT resources to manage and maintain the system. On-premise ERP is an ideal choice for businesses that prioritize complete control over their data and have the necessary resources to support an on-site implementation.
Cloud ERP Software
Cloud-based ERP systems are accessed through the internet, offering flexibility, scalability, and cost-effectiveness. With a cloud-based ERP, your manufacturing data is securely stored and managed on remote servers, eliminating the need for on-site hardware and infrastructure.
This type of system provides the advantage of anytime, anywhere access to your ERP system, as long as you have a stable internet connection. Cloud-based ERP is particularly beneficial for businesses seeking rapid implementation, lower upfront costs, and the ability to scale with their evolving manufacturing needs.
Hybrid ERP
A hybrid ERP system combines elements of both on-premise and cloud-based solutions. This type of ERP offers a balance between control and flexibility.
You can choose to keep some critical data and processes on-premise while leveraging the scalability and accessibility of the cloud for other operations. Hybrid ERP allows businesses to maintain sensitive data on-premise while benefiting from the agility and cost savings of the cloud.
However, it's important to note that integrating and managing data between on-premise and cloud-based environments may introduce additional complexities.
Key Considerations When Selecting ERP Providers
When selecting an ERP system for your manufacturing business, it's crucial to consider various factors that align with your specific requirements. These key considerations include:
- Budget: Evaluate the upfront costs, ongoing expenses, and ROI of implementing the ERP system.
- Scalability: Determine if the ERP system can accommodate your manufacturing growth and expansion plans.
- Industry-Specific Requirements: Ensure the software offers functionality that meets the specific needs of your manufacturing industry.
- Integration Capabilities: Assess the ERP system's ability to seamlessly integrate with other business systems and third-party applications.
- Security: Consider the security measures implemented by the ERP system to protect your sensitive manufacturing data.
- Vendor Reliability: Research the credibility and track record of the provider to ensure a long-term partnership.
By carefully evaluating these considerations and understanding the unique benefits and trade-offs of on-premise, cloud-based, and hybrid ERP systems, you can make an informed decision on the best ERP system for your manufacturing business.
Best Practices When Using ERP for Manufacturing
Successful implementation of Manufacturing ERP requires effective project planning and management, seamless data migration and integration, as well as comprehensive user training and change management.
By following these key strategies, businesses can ensure a smooth transition and maximize the benefits of their ERP system.
Project Planning and Management
Define clear project goals, establish a realistic timeline, allocate appropriate resources, and involve key stakeholders from the beginning. This will help create a shared vision and ensure alignment throughout the implementation process.
Regular communication and collaboration with stakeholders will facilitate timely decision-making and address potential challenges proactively.
Data Migration and Integration
During data migration, it is crucial to accurately transfer existing data into the ERP system, while ensuring compatibility and consistency. A well-planned data migration strategy includes data cleansing, mapping, and validation processes to guarantee the integrity of the data. Additionally, integrating the ERP system with other existing systems and databases is essential for seamless operations and data flow across the organization.
User Training and Change Management
Comprehensive user training is vital to ensure smooth adoption and effective utilization of the ERP system. Providing customized training sessions for different user roles and offering ongoing support will empower employees to use the system effectively and maximize its benefits.
Change management strategies that address employee resistance, communication gaps, and potential workflow disruptions are also essential to mitigate the challenges associated with implementing a new system.
Who Needs Manufacturing ERP Software?
Manufacturing ERP systems are beneficial for businesses of all sizes, ranging from small enterprises to large corporations. These systems provide advanced capabilities that streamline operations and enhance efficiency, allowing manufacturers to stay competitive in their industry.
Various industries commonly utilize ERP systems to optimize their manufacturing processes. Some of these industries include automotive, electronics, pharmaceuticals, food and beverage, and discrete manufacturing.
These sectors have complex production processes, supply chain management, and inventory management requirements that can greatly benefit from the comprehensive functionality of ERP systems.
When Is A Business Ready for ERP Implementation?
Businesses are ready for ERP implementation when they have clearly defined goals, streamlined processes, and a strong desire to optimize operations. Implementing an ERP system is a significant undertaking that requires commitment and preparation.
Before embarking on ERP implementation, businesses should evaluate their readiness based on the following criteria:
- Clearly Defined Goals: A business should have a clear understanding of the goals they want to achieve through ERP implementation. These goals can include improving efficiency, streamlining operations, enhancing data visibility, or overcoming operational challenges.
- Streamlined Processes: Before implementing an ERP system, it is important for a business to have already streamlined their processes as much as possible. ERP systems work best when they can automate and optimize efficient processes. It is crucial to identify and eliminate bottlenecks or inefficiencies in existing workflows before integrating an ERP system.
- Adequate Resources: Implementing and maintaining an ERP system requires financial resources, IT support, and personnel dedicated to the project. Businesses should ensure they have the necessary budget to invest in an ERP system, as well as a reliable IT infrastructure to support its implementation and ongoing maintenance.
- Growth and Operational Challenges: Businesses that have experienced significant growth or face operational challenges such as inventory management issues, production bottlenecks, or data inaccuracies may be prime candidates for ERP implementation. An ERP system can provide the scalability and functionality necessary to overcome these challenges and support the future growth of the business.
10 Tips To Find the Best ERP Solution for Manufacturing Companies
Selecting the right ERP solution is crucial for manufacturing companies aiming to streamline their operations, enhance efficiency, and maintain competitiveness in the fast-paced manufacturing industry.
Finding the best ERP solution involves understanding your company's unique needs, industry requirements, and future growth plans. Here are steps and considerations to help manufacturing companies identify the best ERP solution:
- Assess Your Needs: Begin by conducting a thorough analysis of your manufacturing processes, identifying areas that require improvement, such as inventory management, production scheduling, or customer relationship management. Understanding your core business processes and where you need more visibility, automation, or integration is crucial.
- Define Your Requirements: List the specific functionalities and modules you need from an ERP system, such as real-time analytics, supply chain management, or shop floor control. Consider both your current requirements and those that may arise as your business grows.
- Consider Industry-Specific Solutions: Look for ERP solutions tailored to the manufacturing sector, as these will likely offer the specialized features and capabilities that address common industry challenges.
- Evaluate Deployment Options: Decide whether a cloud-based ERP, on-premise, or a hybrid solution best meets your needs. Cloud ERP systems offer scalability and remote access, making them suitable for companies with distributed operations or those looking for lower upfront costs. On-premise solutions might offer more control and customization.
- Check for Integration Capabilities: Ensure the ERP solution can integrate seamlessly with your existing systems and tools. This integration is vital for maintaining a smooth flow of data across all areas of your business, from financial management to the shop floor.
- Scalability and Flexibility: Choose an ERP system that can grow with your business. The best manufacturing ERP solution will be scalable to accommodate new processes, additional users, and expanding operations without significant overhauls.
- Vendor Experience and Support: Select a vendor with a proven track record in the manufacturing industry and a strong support system. Look for vendors who offer comprehensive training, ongoing support, and customization services to help you maximize the benefits of your ERP system.
- Request Demos and Conduct Pilot Tests: Before making a final decision, request demos to see the ERP system in action. Consider conducting a pilot test with a shortlist of ERP solutions to evaluate their performance in real-world scenarios relevant to your manufacturing operations.
- Consider Total Cost of Ownership: Look beyond the initial purchase price to consider the total cost of ownership, which includes implementation costs, training, customization, and ongoing support. A cost-effective ERP solution offers a balance between upfront costs and long-term value.
- Seek Feedback and Recommendations: Consult with peers in the manufacturing industry, read case studies, and seek recommendations from other manufacturing companies. Learning from the experiences of others can provide valuable insights into the strengths and weaknesses of different ERP solutions.
Final Thoughts
To wrap up, the implementation of ERP systems can greatly benefit businesses in the manufacturing industry. These powerful tools have the ability to optimize production processes, enhance supply chain management, and improve decision-making.
By streamlining operations, improving efficiency, and enabling data-driven decision-making, manufacturing ERP systems pave the way for success in a highly competitive marketplace.
These ERP systems, whether on-premise, cloud-based, or hybrid, need to be carefully chosen to meet the specific needs and challenges of a business. Effective implementation, including strategic planning, data integration, and training, is essential.
Manufacturing ERP systems are essential for streamlining operations and laying the groundwork for future expansion and innovation. By keeping up with industry trends and effectively utilizing manufacturing ERP systems, businesses can secure continuous success and differentiate themselves in a highly competitive market.
Tailor provides manufacturing companies with ERP solutions that are both adaptable and scalable, catering to the dynamic needs of modern manufacturing. These solutions are designed to grow with your business, ensuring that as your manufacturing processes become more complex or your production volume increases, your ERP system can handle the changes with ease.
Whether you're dealing with intricate supply chains, diverse product lines, or specific compliance requirements, Tailor's ERP solutions are completely customizable to meet these specific demands.