How ERP Software Is Revolutionizing Inventory Management for Retail Stores
Retailers don't have it easy these days. For starters, they have the unenviable task of constantly striking the right balance between stock availability and demand, ensuring that popular items are always in supply while avoiding overstocking less desirable products, which is crucial for a positive retail experience. Traditional methods of inventory management, which often rely on manual tracking and disconnected systems, lack the key features necessary in today’s fast-paced, data-driven retail operations environment.
This is where enterprise resource planning (ERP) software comes into play — offering retail stores a comprehensive solution to revolutionize their warehouse management and inventory management processes through data-driven decisions.
Understanding ERP and its role in retail
ERP systems are integrated software platforms that manage a company’s core business processes—from HR and financial management to supply chain and inventory management—all within a single system. For retailers, an ERP system is particularly valuable as it connects various aspects of the business, from sales and customer service to procurement and logistics. By centralizing these functions, ERP systems provide a real-time view of business operations, which can lead to better decision-making and increased efficiency.
In retail, inventory management is one of the most critical areas where ERP systems can make a significant impact. An effective ERP tracks inventory levels and automates various processes, such as reordering, supplier management, and sales forecasting. This level of integration and automation empowers retailers to maintain optimal inventory levels, reduce costs, and ultimately improve customer satisfaction.
Streamlining inventory tracking
One of the most significant advantages of using an ERP system in retail is the ability to track inventory in real time across all sales channels, whether in-store or online. This is especially important in today’s omnichannel retail environment, where customers expect seamless shopping experiences regardless of where they choose to make a purchase.
With an ERP, retailers have visibility into their inventory levels at any moment across all locations, enhancing their overall supply chain management capabilities. This real-time tracking eliminates the guesswork associated with manual inventory management, where stock discrepancies are common due to human error or delayed data entry. By providing accurate, up-to-date information on stock levels, ERPs help retailers make informed decisions about reordering, promotions, and stock transfers between locations.
For example, if a popular item runs low at one store, the ERP can automatically trigger a transfer from another location where the item is in surplus. This ensures that customers always find what they need, reducing the likelihood of lost sales due to stockouts.
Minimizing stockouts and overstocks
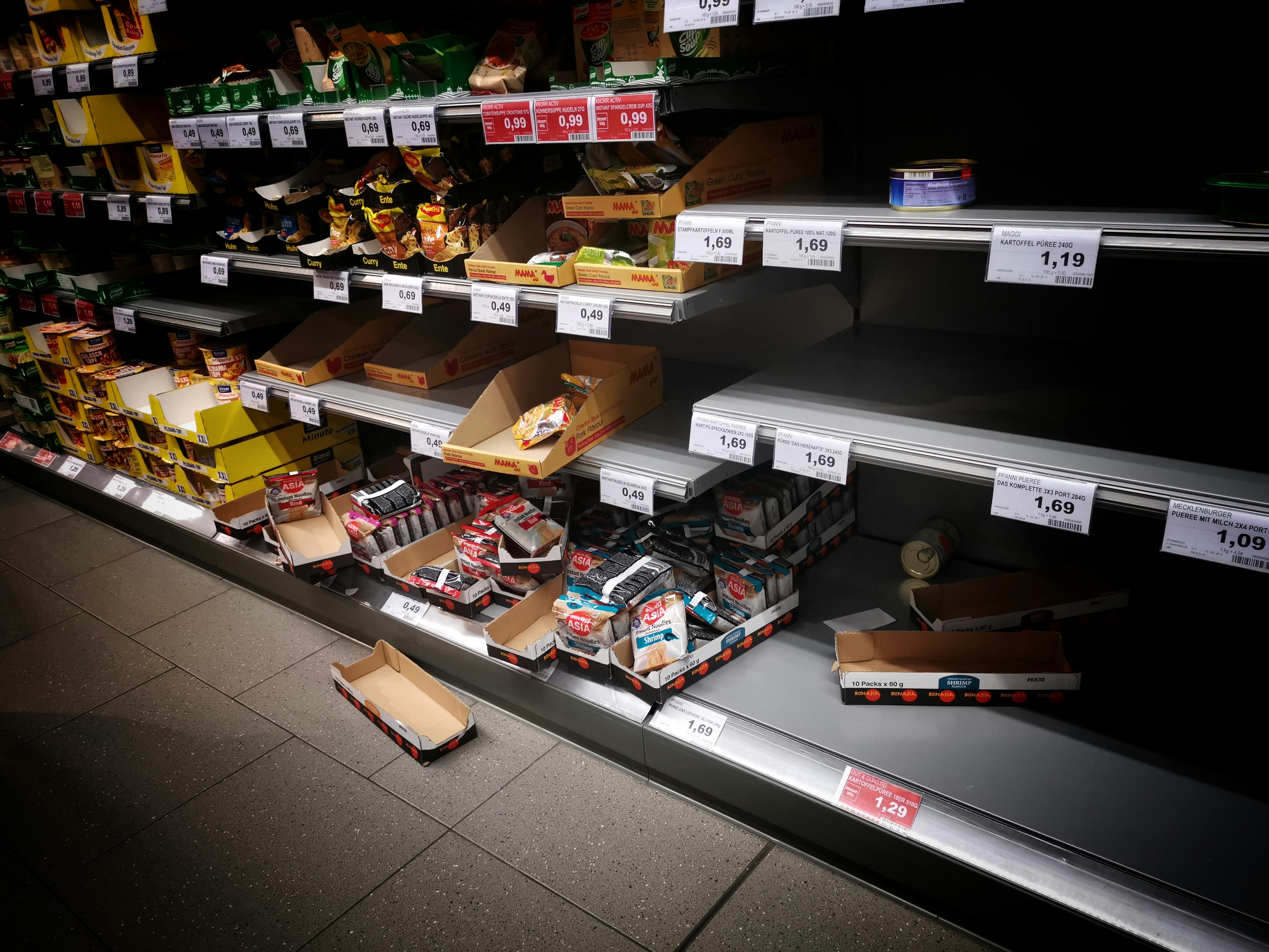
Stockouts and overstocks are two of retailers' most common inventory management challenges. Stockouts occur when an item is out of stock, leading to missed sales opportunities and a negative customer experience. Overstocks, on the other hand, tie up capital in unsold inventory, increasing storage costs and the risk of obsolescence.
ERPs help retailers maintain the proper balance by providing tools for automated reorder points and demand forecasting. These features allow retailers to set minimum stock levels for each product, automatically triggering a reorder when inventory falls below a certain threshold. This prevents stockouts by ensuring that popular items are always available for purchase.
Demand forecasting, another powerful feature of ERP systems, uses historical sales data and market trends to predict a product's future demand. By analyzing this data, retailers can make more accurate purchasing decisions and avoid the risk of overstocking. For example, an ERP might identify that a particular product sells better during certain seasons or in specific regions, allowing the retailer to adjust their inventory levels accordingly.
Enhancing supplier relationships and replenishment
Effective inventory management for retail businesses isn’t just about what happens within the store; it also involves managing relationships with suppliers to ensure timely and cost-effective stock replenishment. ERP software excels in this area by automating and streamlining supplier management processes.
With an ERP, retailers can automate purchase orders based on real-time inventory levels and sales data, speeding up the ordering process and reducing the risk of human error. Retailers can also use the system to track supplier performance, including delivery times and order accuracy, which makes it easier to identify and address any issues that could impact their inventory levels.
ERPs also have tools for managing supplier contracts and pricing agreements, allowing retailers to negotiate better deals and optimize their procurement processes. For instance, a retailer might use their ERP to identify opportunities for bulk purchasing or to consolidate orders from multiple locations, reducing shipping costs and improving overall supply chain efficiency.
Real-time data and analytics for smarter decision-making
In today's retail environment, data is king. Accessing and analyzing real-time data is crucial for making informed decisions that drive business success. ERP platforms provide powerful analytics tools that give retailers deep insights into their inventory, sales, and operations.
With an ERP, retailers can generate detailed reports on inventory turnover, slow-moving items, and sales trends. This is invaluable information for making strategic decisions about which products to promote, which to discount, and which to discontinue. If, for example, a retailer notices that a particular product is consistently underperforming, they might decide to stop stocking it and replace it with a more popular item.
ERPs also enable retailers to forecast demand more accurately, reducing the likelihood of stockouts and overstocks. By analyzing historical sales data and market trends, retailers can anticipate changes in customer demand and adjust their inventory levels accordingly. This helps maximize sales and reduces the risk of holding excess inventory that could become obsolete.
The role of ERP in managing multi-location inventory
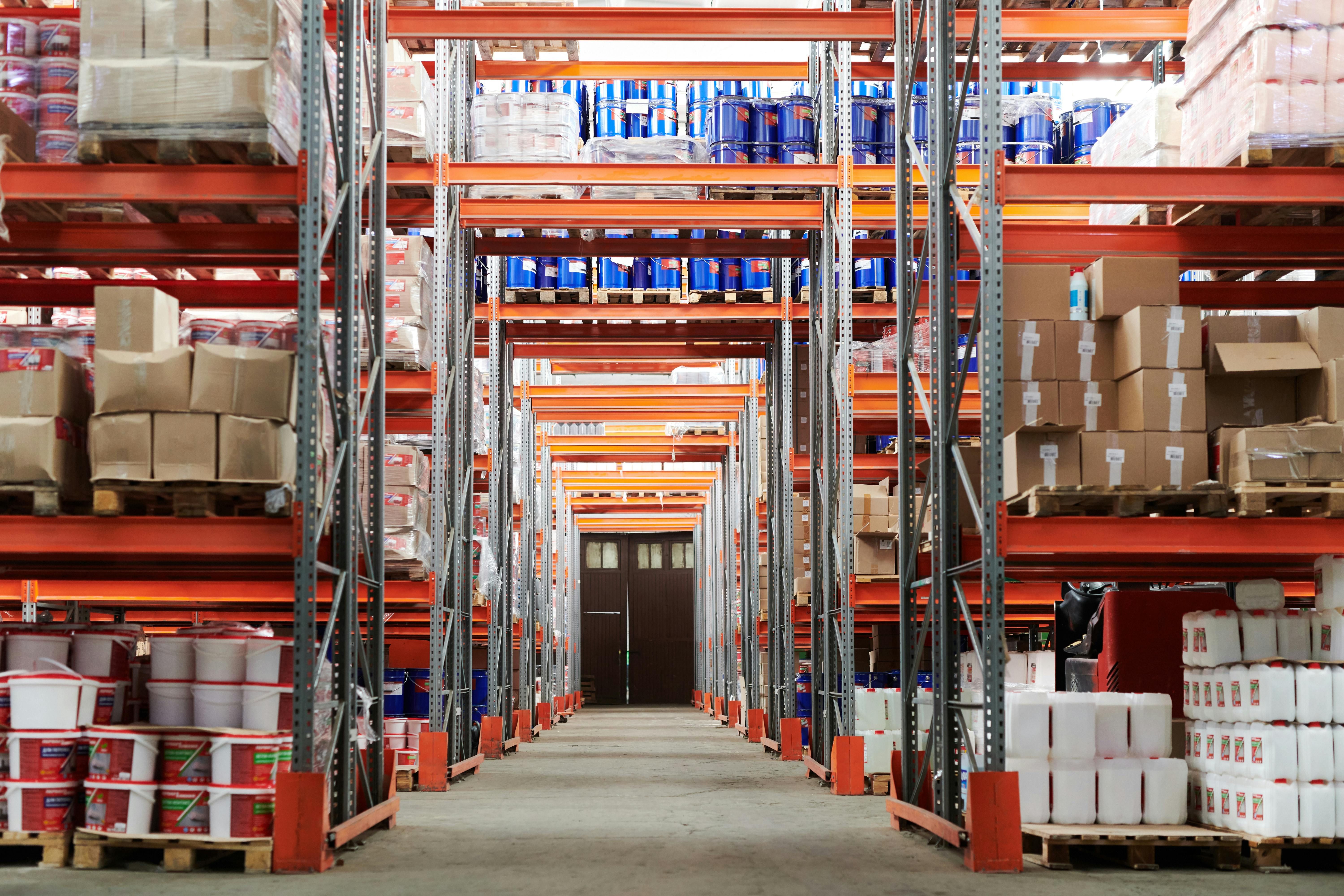
For retailers with multiple store locations, managing inventory can be particularly challenging. Without a centralized system, tracking stock levels across different locations can be difficult, leading to inefficiencies and lost sales opportunities. ERP software solves this problem by providing a unified, single source platform for managing inventory across all stores.
With an ERP, retailers can quickly transfer inventory between locations to meet demand. So, if one store runs low on a particular item, the system can automatically initiate a transfer from another location where the item is in surplus. This ensures that all stores are adequately stocked, reducing the risk of stockouts and improving customer satisfaction.
ERPs also provide real-time visibility into inventory levels at each location, allowing retailers to make informed decisions about where to allocate stock. This is particularly important for retailers with regional or seasonal variations in demand, as it enables them to optimize their inventory levels based on local market conditions.
Reducing manual errors and labor costs
Manual inventory management processes are prone to errors — bad things like miscounting items, entering incorrect data, or failing to update records in a timely manner. These errors can have serious consequences, leading to stock discrepancies, lost sales, and increased labor costs.
ERP software eliminates many of these manual tasks by automating inventory management processes. For example, instead of manually counting stock levels and entering the data into a spreadsheet, staff can use barcode scanners or RFID technology to update inventory records in real time. This reduces the risk of errors and frees up staff to focus on more value-added activities, like assisting customers or merchandising the store.
ERPs can also help retailers reduce labor costs by automating routine tasks. For instance, automated reordering and supplier management processes mean that staff no longer need to manually create purchase orders or follow up with suppliers. Instead, the ERP can handle these tasks automatically, allowing staff to focus on more strategic activities that contribute to the store’s success.
Tailor: A better way to manage your inventory
Put simply, effective inventory management is critical to success, especially in today’s ultra-competitive retail environment. ERP software offers retailers a powerful solution for streamlining inventory management processes, reducing costs, and improving operational efficiency. By providing real-time visibility into inventory levels, automating routine tasks, and offering advanced analytics capabilities, ERP systems enable retailers to make smarter decisions and stay ahead of the competition.
For retailers looking to revolutionize their inventory management processes, Tailor's headless ERP offers an innovative, state-of-the-art solution. Whether you’re a small shop looking to scale your operations or a large chain seeking to optimize your supply chain, our ERP technology can provide the tools and insights you need to succeed in today’s fast-paced, data-driven retail environment.
Ready to take your inventory management to the next level?
Schedule your demo today.